This style of printing is not a new kid on the block, but is as fascinating as ever to see the process unfold in front of you.
Stamp:


Photo Source: Fizzy Goblet
To make the ‘ink’ for block-printing, a combination of lime, gum, water and very smooth mud (specifically chosen from river beds around Akola, Rajasthan) are dunked together in a large container. The next day, this 60kg mixture is made into a paste after three rounds of stomping, mixing and kneading with one’s feet. This is called the daboo or mud-resist style of block printing.
It’s kind of like the process of grape-stomping to make wine, but admittedly less glamorous.
Print:
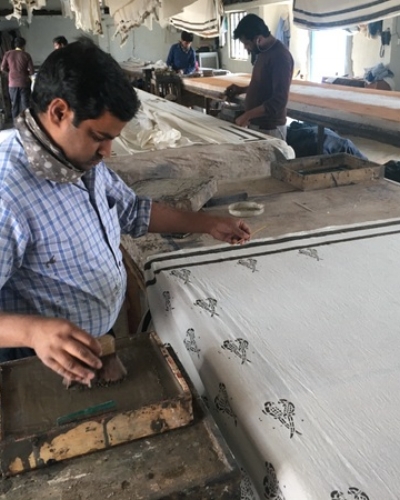
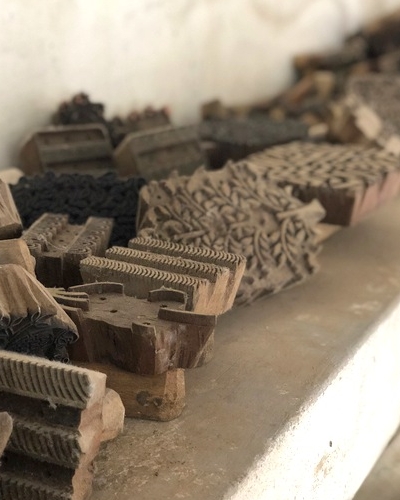
Photo Source: Fizzy Goblet
A nine-yard fabric is pinned to a long table, over a layer of sawdust to ensure that it stays in place and absorbs the excess ink (mud). The artist then dips the wooden block in the stamp pad and prints it repeatedly and carefully all over the cloth.
The mud is used to keep the pattern in place (be it a flower or a parrot) while it goes through the next step: dyeing.
Dye:
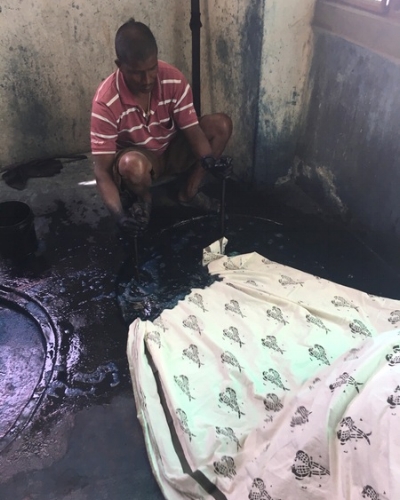
Photo Source: Fizzy Goblet
Depending on the intended background colour (blue in this case), the cloth is dipped and soaked in 9-feet-deep indigo wells with wooden sticks. The longer the cloth is soaked, the deeper the blue will be. The mud-blocked print stays on through the process. In the case of other colours, Aavaran uses Manjusha for a brown colour, haldi for a yellow, and more natural dyes.
Rinse & Repeat:

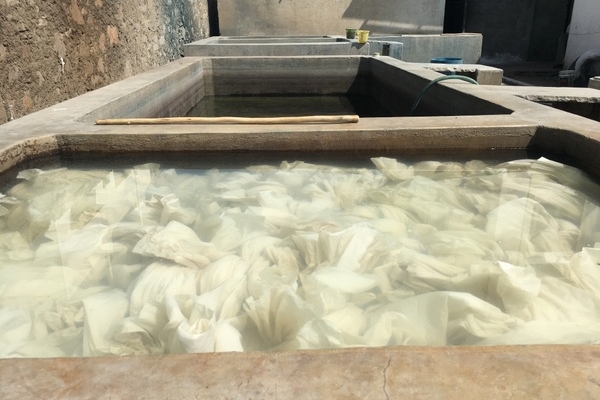
The colour of the cloth dries under the sun, and is then taken through the printing and dyeing steps again. Finally, when different blocks are used to complete the pattern on the cloth, dyed again and dried one last time, the cloth is soaked in water overnight.
The mud, which was holding the pattern in place, is then removed from the cloth to reveal the white left over print.
This cloth is then bundled up, taken to the tailor’s room where your next favourite dress, kurta or blouse piece is stitched into action.
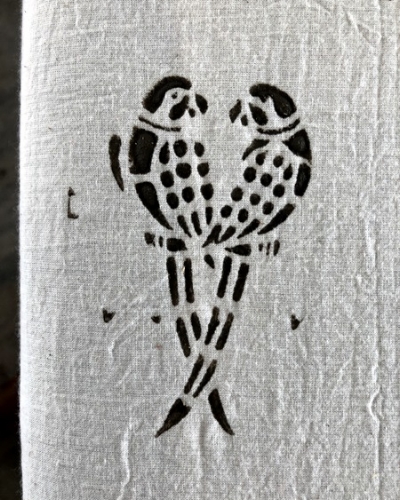
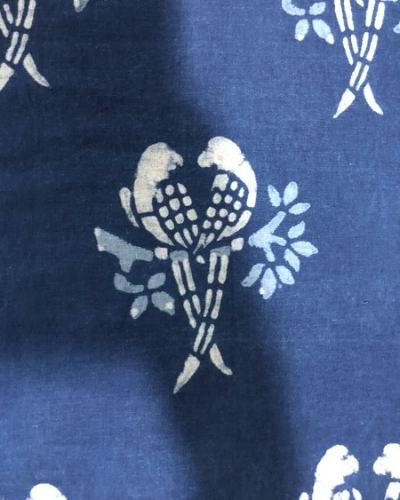
Photo Source: Fizzy Goblet
Bhavika Govil is a writer made up of equal parts popcorn and puns. see her illustrations here.